Staying Comfortable with Less
Frank Crawford, P.Eng., looks through his triple-pane windows at mounds of fresh snow. Despite the frigid temperature outside, Crawford is warm behind the thick, insulated walls of the home he designed and built in 2015 following Passive House standards. His house requires very little heat to stay warm and uses only a scant number of small electric resistance heaters—a feat that seems almost impossible in frosty Alberta winters. Crawford, his family, and secondary suite tenants live in one of the first homes built to the international Passive House standard in Alberta, and he has helped many others achieve similar levels of performance and comfort in his role as a certified passive house designer and tradesperson.
The Passive House model of construction uses five key techniques to achieve comfort while using very little energy. A thick layer of insulation on the exterior walls creates a strong barrier—referred to as the building envelope—between the outdoors and indoors. Airtightness reduces drafts and heat loss throughout the building and is verified during construction by finding and patching all air leaks. High-performance windows reduce heat loss. Strategically placed overhangs allow the sun in during the winter and block the sun in the summer—like SPF for your house. Energy efficient ventilation systems capture waste heat from exhausted air and preheat fresh air from outside to circulate throughout the building. Finally, constructing the exterior walls to avoid unnecessary heat loss through leakage or infiltration further reduces energy usage. By implementing these techniques in combination, newly constructed Passive House–certified buildings use about 80 per cent less energy than similar traditional buildings, with minimal added construction cost.
Crawford and his family knew they didn’t want to live long term in their 70-year-old house due to high utility costs, minimal insulation, single pane windows, and several drafts—they decided to move and start from scratch. They decided to look at energy efficient building system options for their home and came across the Passive House standard. “If the goals include comfort, quiet, no drafts, less dust, great indoor air quality, low utility bills, and long-term durability, you're building a passive house or high-performance building.” There is also a retrofit program from Passive House—called EnerPHit—that applies the same five key techniques to existing buildings, achieving energy savings between 75 and 90 per cent.
Working together
Stuart Fix, P.Eng., a mechanical engineer and the principal of APEGA permit holder ReNü Engineering, developed an enthusiasm for Passive House methods and viewpoints while obtaining his master’s degree in building science, with a focus on optimizing the building envelope. ReNü Engineering pioneered Passive House methods in Alberta, working on the first Passive House–certified home and commercial building. Fix’s mechanical engineering background in thermodynamics and his building envelope specialty pair well on projects where the interconnection of mechanical systems and the building envelope drives design decisions. Passive House is different from other sustainability programs because it is performance based. “Passive design is steadfastly focused on conservation—it doesn't worry about anything else. It's very focused on reducing energy.”
In a traditional build, the architect and each engineering discipline complete the necessary tasks for their design separately, working in coordination only where their respective systems overlap. However, in Passive House construction, the architect and engineers work closely together from day one of design to limit the amount of energy the building will use. Using specialized software, engineers create a digital replica of the building to determine how much energy it will use throughout the year. From there, they determine if the performance is low enough to achieve certification or if they need to refine the design. The digital model also helps find weak spots in the construction of the exterior walls, enabling them to further reduce energy usage.
Creative solutions
Trevor Butler, P.Eng., had some experience with Passive House design projects when he came to Canada from the U.K. more than a decade ago. “As a profession, as an industry, we're incredibly creative if we're given a challenge.” He has now completed hundreds of passive design projects across Canada, including several in Alberta, such as the McMurray Métis Cultural Centre in Fort McMurray, which is a net-zero-carbon cultural centre featuring biomass (wood) fuel, highly efficient HVAC systems, and large tubes installed underground to heat or cool incoming air from outside.
With the Passive House program in Alberta slowly catching on, we’re still in the education stage of adoption. One organization helping to spread the word is the Smart Sustainable Resilient Infrastructure Association, an Edmonton-based organization focused on driving change towards an energy-efficient built environment in Alberta through collaboration, demonstration, and pairing projects with funding opportunities. Crawford, Fix, and Butler use their passive design enthusiasm and construction experience to continue pushing the envelope of what is possible in Alberta, making the province more energy efficient—one building at a time.
Featured in this article
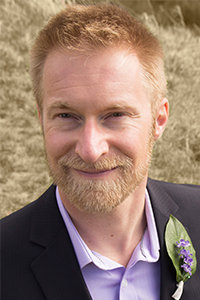
Frank Crawford, P.Eng.
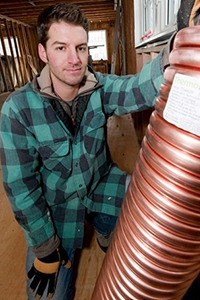
Stuart Fix, P.Eng.
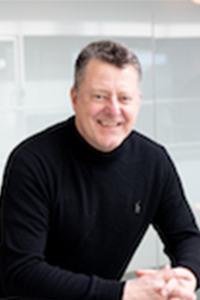
Trevor Butler, P.Eng.