Refining Recycling: A Practical Dream
Have you ever heard the saying, "If you can dream it, you can do it"? A common nicety printed on motivational posters—pinned, sun-bleached, and forgotten—on classroom walls.
Dr. Rafiq Ahmad, P.Eng., proves the saying isn't simply a nicety. He is an illustration of it in action. His grandiose dreams are fruits of practicality he has the knowledge, the drive, and the lab to make them a reality.
Dr. Ahmad’s latest dream is one in a long line of epiphanies conceived to improve industrial processes, and consequently the world around him. His newest reverie is to make recycling—a long-held conundrum of city planners and environmentalists alike—more effective.
Disillusioned by all the plastics in Alberta, and the fact that recycling efforts often cost more than producing new materials, Dr. Ahmad came up with a vision for new, intelligent recycling processes. His process takes plastics and turns them into entirely new, useful products. His process also makes economic sense. “Only nine per cent of Canadian plastic is currently recycled, and recycling processes are not very sustainable,” Dr. Ahmad explains.
"We want to create new, cheaper processes and a bigger impact by combining different technologies. We can do this because we are one of the labs in the world pioneering artificial intelligence and digitization."
Dr. Ahmad runs the Laboratory of Intelligent Manufacturing, Design and Automation (LIMDA) at the University of Alberta, where his team focuses on designing intelligent systems for manufacturing and production. His team is one of the groups spearheading the fourth industrial revolution (Industry 4.0)—the first being steam engines, the second electricity, the third automation, computers, and robots. The fourth incorporates intelligence and connectivity—making machines smart, connected via the internet, and able to make data-based decisions in a process or system.
Productively processing plastics
"The goal is to automate the entire recycling process—make it intelligent. What I envision is a complete plastic manufacturing facility.” Dr. Ahmad foretells consumers would bring in plastic products, like water bottles, and the fully roboticized and automated facility would use a conveyor, a robotic system, and a camera imaging system with artificial intelligence to detect the types of plastic in the bottles and sort them.
After sorting, plastic would get cleaned and shredded, then refined to remove impurities. The next automated step would transform the shredded plastics into filaments or pellets, creating a viable material for 3-D printing or injection molding.
“My goal is one day people just think about a product they want, find out how many plastic bottles it takes to make the product, bring them to the recycling centre, and shortly after can take their 3-D printed plastic product home.”
His system would fulfil a need for the consumer and help keep plastics from returning to the environment needlessly. You need a new spatula? Save your soda bottles.
His team at LIMDA is beginning the process of building his dream by exploring which plastics can mix to generate new products, with a focus on how many times a particular plastic can go through the recycling process. Driven by his profound interest in efficiency, Dr. Ahmad is hoping to mix plastics never successfully combined before and increase the number of times a product can be recycled. “If you can recycle a particular plastic five times, why not ten times by adding more materials? We can actually increase the life of a particular product before it goes to the environment and causes harm.”
Possibilities borne of plastic
He says figuring out how to mix different plastics to create a viable 3-D printing material is a challenge, but his team aims to meet it—and create a stronger plastics post-recycling process. “How can we improve these materials to make them more durable for extreme weather conditions in Alberta, for example. We want these products to stay usable for longer periods of time.”
Dr. Ahmad explains this type of intelligent recycling creates endless opportunities for waste optimization across many industries and will enhance the circular economy.
Besides recycling, the team at LIMDA focuses on “giving life to end-of-life products” by working on systems to intelligently repair downhole tools used for oil extraction. Using robotic machining and 3-D printing, they repair parts while ensuring the products and uses are the same. They also remanufacture products, giving industry tools and parts completely new functionalities, often in a different industry altogether. Dr. Ahmad is excited to take a step to become a leader in a more sustainable and forward-thinking recycling practice.
Besides developing tools and methods to digitally transform manufacturing systems, the team at LIMDA concentrates on the human side of industry—training people to safely use these new tools, technologies, and processes. The human aspect of control in these systems is paramount, according to Dr. Ahmad. “I use this type of intelligence for helping society and leverage these systems to increase the safety of humans. A human should always be able to intervene and change any decision a machine makes.”
In the future of plastic processing, maybe the human decision will be choosing a new spatula, protractor, or Frisbee when you drop off your bottles at the recycling station. Or maybe it will be an option for shelter for someone who doesn’t have a home, a new set of soles for some worn shoes, or the perfect addition to a budding engineer’s invention—the next practical dreamer in Alberta.
Featured in this article
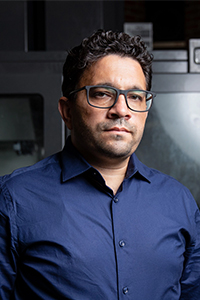
Dr. Rafiq Ahmad, P.Eng.